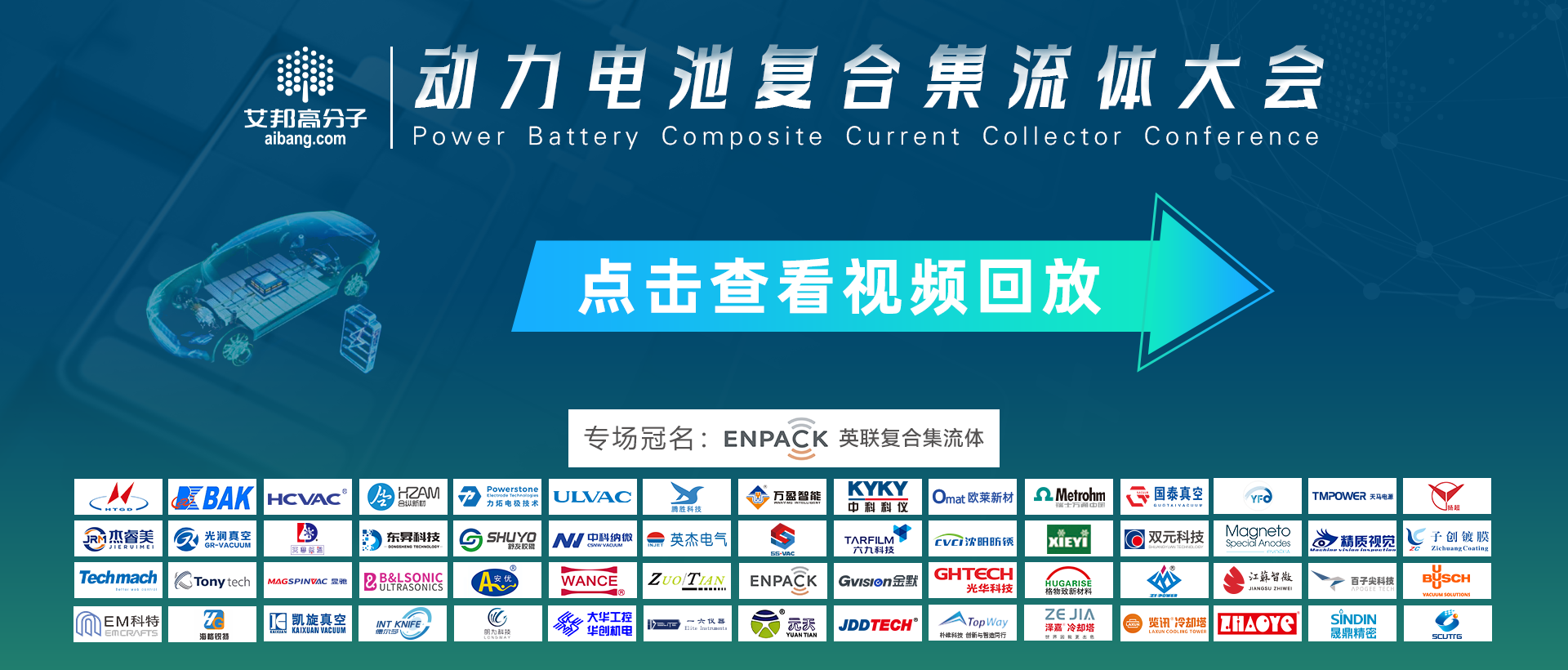
凭借“降本+高安全”的核心优势,复合集流体开启了对传统集流体的产业化替代,成为锂电创新发展的一大趋势。作为全球最大的新能源装备服务商,先导智能现已推出复合铜箔、复合铝箔创新制造方案,为锂电行业的材料变革贡献先导力量。
相较应用纯铜、纯铝的传统集流体,应用了高分子材料和金属的复合集流体具备高安全、长寿命、低成本、强兼容等突出优势,在企业降本需求下正走向高成长赛道。研报显示,2025年锂电池装机量将预计达到1.5TWh,复合集流体市场渗透率有望达到20%,到2030年将突破千亿级市场。然而,当前行业整体制造工艺以及最终产品的多项关键指标仍需提升。
作为全球最大的新能源装备服务商,先导智能始终以研发创新为核心,致力于成为全球性创新企业。依托先导研发团队的深厚科研力量,先导现推出了复合集流体创新制造方案,相关设备现已获得了客户订单,并得到了来自客户的高度认可。
复合铜箔的核心成本优势在于节省金属材料,然而由于行业处于发展初期,复合箔材制造存在箔材穿孔、方阻大、铜膜结合力低等工艺难题,综合制造成本仍然较高。
面对系列工艺难题,先导提出“磁控溅射+水电镀”创新型解决方案,有效提升了箔材良率与设备稼动率,实现了生产成本的有力节约,有助于增强客户的差异化竞争力。
通过对多项自研工艺的应用,先导磁控溅射镀膜机有效能够有效保证产品良率,降低加工成本。设备采用了自研基材热管理方案,通过对杂散电子逃逸路径的提前规划,实现了对基膜升温的有效控制,升温幅度仅为传统方式的40%;创新智能闭环控制,镀膜厚度公差小于5%。
此外,设备更突破了现有溅射沉积的速率上限,沉积速率达到1600 nm.m/min,在30—50nmnm沉积厚度时,卷绕速度可达到24—48m/min。
在保证生产质量与效率的同时,先导方案更能够有效节约加工成本:借由创新的磁场设计,在使用传统靶材时,靶材利用率依然高达85%;自研真空结构,在抽真空环节更能实现40%的能耗节约。
在水电镀增厚环节,先导创新方案有效提升了复合铜箔的产品良率、制造效率,并首创实现了智能化管理。设备采用了专利夹持导电系统,电镀效率提升30%,卷绕速度可达20m/min。
依托先导智能研发团队,产品独创超声波水洗工艺,使得膜面洁净度取得了20%以上的提高,同时优化切废边环节的铜粉管理,在长期使用中更能保障箔材的生产质量。设备更首创智能化系统设计,实现智能运维管理及工单管理。
在成本控制上,设备创新采用了在线溶纯铜+不溶性阳极设计,在实现设备稼动率提升的同时,更能有效降低氧化铜粉消耗。经测算,每条生产线每年能降低材料成本约100万元。
高安全、高比能是复合铝箔集流体的核心优势,然而由于行业仍处发轫期,集流体成品存在材料方阻大、膜层结合力低、成品针孔率居高难下等工艺难题。依托锂电产业深厚的技术和工艺积淀,先导智能在复合铝箔制造领域自研出完备的制造方案,设备经客户验证,现已获得首批订单。
先导高真空蒸发镀膜机采用了自研双蒸发源结构,双面送丝,双倍蒸发量,搭配采用特殊涂层工艺和静电结构的冷辊,实现了镀膜面密度和面均匀性的大幅提升,并达到了大于60%的铝丝利用率,卷绕速度达到48m/min。设备应用了智能闭环控制,镀膜厚度公差≤5%,创新变频技术,抽真空的环节更能降低50%的能耗。
新能源产业的发展为电池行业的技术革新提供了源源不断的动力,从电池的材料端到结构端,全行业积极寻求创新,以求获得能量密度更高、成本更低的产品。未来,先导智能将持续加大对复合集流体的研发与投入,助力储能电池企业降本增效,取得更强的市场竞争力。
新能源汽车的快速发展带动了动力电池的高速增长。动力电池生产流程一般可以分为前段、中段和后段三个部分。其中,前段工序包括配料、搅拌、涂布、辊压、分切等,中段工序包括卷绕/叠片、封装、烘干、注液、封口、清洗等,后段主要为化成、分容、PACK等。材料方面主要有正负极材料,隔膜,电解液,集流体,电池包相关的结构胶,缓存,阻燃,隔热,外壳结构材料等材料。
为了更好促进行业人士交流,艾邦搭建有锂电池产业链上下游交流平台,覆盖全产业链,从主机厂,到电池包厂商,正负极材料,隔膜,铝塑膜等企业以及各个工艺过程中的设备厂商,欢迎申请加入。
长按识别二维码关注公众号,点击下方菜单栏左侧“微信群”,申请加入群聊