随着新能源汽车技术创新的持续进步,其电池管理系统(BMS,Battery Management System)也进入了快速发展的跑道。由于各厂商对封装密度的要求越来越高,BMS中传统的线束方案亦开始逐步被集成母排(CCS,Cell Contacting System)方案所替代。有别于线束中的NTC温度传感器,CCS中的FPC(柔性电路板,Flexible Printed Circuit)一般采取片式NTC热敏电阻,以实施新能源电池的温度监控。
FPC为什么能成为BMS中传统线束的替代大热门呢?这是因为:
一、高度集成化
采用FPC是为了更好地节省空间,同时改善BMS内部结构。区别于线束的多个NTC传感器集成,一条FPC上即可装配BMS所需的主要元器件,能帮助BMS往轻量化、智能化的方向稳步前进。
二、高折弯强度
FPC的主要基材为柔性覆铜板,可根据安装位置进行不同程度的折弯、卷绕、叠迭,在BMS中的贴合度极高。
三、测温组件小型化
线束主要采用NTC温度传感器进行实时温度监测,复杂的结构使BMS的空间利用难以达到最大化。FPC采用片式NTC热敏电阻进行温度采集及监测,其小尺寸可更接近被监测单元且简化安装结构。
四、提高自动化生产
线束需要人工操作安装,不仅人工成本高,而且装配效率低。采用FPC能实现自动化作业,摈弃繁琐的线束组装同时简化生产流程。
综上所述,FPC打破工艺局限性、规整安装布局,是取代线束的主要优势。而片式NTC热敏电阻的加入,更是提高了该优势:
一、无引线封装迎合组装需求,提高FPC集成度;
二、参数支持定制,且尺寸可根据客户选择提供0201、0402、0603、0805等;
三、片式NTC热敏电阻适合表面贴装,可满足客户SMD需求及规模化的批量生产。
来源:Exsense爱晟电子

新能源汽车的快速发展带动了动力电池的高速增长。动力电池生产流程一般可以分为前段、中段和后段三个部分。其中,前段工序包括配料、搅拌、涂布、辊压、分切等,中段工序包括卷绕/叠片、封装、烘干、注液、封口、清洗等,后段主要为化成、分容、PACK等。材料方面主要有正负极材料,隔膜,电解液,集流体,电池包相关的结构胶,缓存,阻燃,隔热,外壳结构材料等材料。 为了更好促进行业人士交流,艾邦搭建有锂电池产业链上下游交流平台,覆盖全产业链,从主机厂,到电池包厂商,正负极材料,隔膜,铝塑膜等企业以及各个工艺过程中的设备厂商,欢迎申请加入。
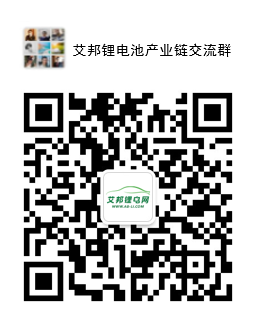
长按识别二维码关注公众号,点击下方菜单栏左侧“微信群”,申请加入群聊