一、CCS:新能源电池的“神经中枢”,为何需要“精准焊接”?
CCS集成母排由FPC(柔性电路板)、铜/铝巴、采集线、温度传感器等部件组成,其核心功能是:
电连接:将多个电芯串联/并联,形成电池模组;
信号采集:实时监测每个电芯的电压、温度,反馈给BMS(电池管理系统),防止过充/过放或热失控;
结构支撑:固定电芯,保护内部线路免受振动或碰撞损伤。
由于CCS直接关联电池的安全性与寿命,其焊接工艺需满足三大严苛要求:
✅ 低电阻:焊接点电阻需极低(接近0),避免能量损耗;
✅ 高可靠性:耐受电池充放电循环中的热膨胀与机械应力;
✅ 微小化:适配电芯的超薄极耳(厚度仅0.1-0.3mm),避免焊接变形或烧穿。
传统焊接(如激光焊、电阻焊)在处理CCS时,常面临“精度不足”或“热损伤”的难题:
-
激光焊易因热输入过大导致极耳熔穿;
-
电阻焊则可能因压力不均造成虚焊。
而超声波焊接凭借“冷加工”特性,完美契合了CCS的精密需求。
二、超声波焊接:CCS制造的“精密缝合术”,如何破解行业痛点?
超声波焊接的核心原理是:通过高频振动(20-40kHz)与压力,使待焊材料表面分子剧烈摩擦,产生局部热量(约为材料熔点的1/3),在不熔化母材的情况下实现分子级熔合。
这种“冷焊接”特性,恰好解决了CCS的三大挑战:
1. 低电阻、高可靠性:破解电连接难题
在CCS的铜/铝巴焊接中,传统工艺常因氧化层残留或熔深不均导致接触电阻升高(可能增加5-10%的能量损耗)。而超声波焊接的高频振动能主动破除材料表面氧化层,使清洁的金属原子直接接触,形成冶金结合。实测数据显示,超声波焊接的铜铝搭接电阻仅为传统钎焊的1/5,且抗疲劳性能提升30%以上。
2. 微小化、无损伤:适配超薄极耳与精密传感器
CCS的采集线(多为0.1-0.3mm的铜/铝箔)与FPC线路板焊接时,对热输入极其敏感。超声波焊接的能量集中在接触点(面积仅0.5-2mm²),且焊接时间短(0.1-0.5秒),几乎不产生热扩散,避免了线路板因高温变形或烧蚀。例如,在某新能源车企的CCS产线中,超声波焊接的FPC采集线良率高达99.8%,远超传统工艺的95%。
3. 高效、环保:降低制造成本与碳排放
超声波焊接无需焊丝、助焊剂或保护气体,单焊点能耗仅为激光焊的1/3,且设备占地面积小(仅需传统焊接设备的1/2)。以某电池厂为例,采用超声波焊接后,单条CCS产线的年耗电量减少40%,耗材成本降低60%,同时避免了化学试剂的污染,完美契合“双碳”目标。
三、从实验室到产线:超声波焊接在CCS中的典型应用场景
在实际生产中,超声波焊接已深度渗透至CCS的多个关键环节,以下是几个代表性案例:
案例1:铜铝巴与FPC的“异种金属焊接”
新能源电池的铜巴(正极)与铝巴(负极)需通过FPC线路板连接,而铜铝的热膨胀系数差异大(铜17×10⁻⁶/℃,铝23×10⁻⁶/℃),传统焊接易因应力导致开裂。超声波焊接通过高频振动软化材料,使铜铝界面形成“过渡层”,成功解决了异种金属焊接难题。广东力王的“超声波焊接CCS集成母排”专利(CN222940971U)便采用此技术,取消了传统镍片转接,成本降低20%以上。
案例2:采集线与铝巴的“多股细线焊接”
CCS的电压/温度采集线通常由多股0.05mm²的铜/铝细线组成,传统焊接易导致“散线”或“虚焊”。超声波焊接的高频振动能均匀压缩多股细线,同时破除表面氧化膜,形成致密的焊接点。某头部电池厂实测显示,超声波焊接的采集线拉力可达5N以上(行业标准仅3N),大幅提升了信号采集的稳定性。
案例3:NTC温度传感器的“无损焊接”
NTC(负温度系数热敏电阻)是CCS的核心传感器,需与FPC线路板精密焊接。超声波焊接的低热量输入(峰值温度<150℃)避免了NTC的温敏材料失效,同时焊接点的“微凸结构”增强了接触可靠性。某高端电动车品牌的电池系统中,采用超声波焊接的NTC传感器故障率从0.3%降至0.01%,显著提升了热失控预警的准确性。
四、未来趋势:超声波焊接如何“赋能”CCS的智能化升级?
随着新能源汽车向高能量密度、长寿命方向发展,CCS的设计也在向“更薄、更密、更智能”演进,这对超声波焊接提出了新的挑战与机遇:
1. 高频化与精密化:适配更薄的极耳与更小的焊点
当前主流超声波焊接频率为20kHz,未来随着极耳厚度降至0.05mm以下,60kHz以上的高频焊接技术将成为趋势。高频振动能更精准地控制能量输入,减少对母材的损伤,同时支持0.2mm²以下的超小焊点,满足微型化设计需求。
2. 智能化与数据化:焊接过程的“全链路监控”
新一代超声波焊接设备已集成AI算法与传感器,可实时监测焊接压力、振幅、能量等参数,并通过机器学习优化工艺。例如,某设备商的“智能焊接系统”能自动识别材料厚度与表面状态,动态调整焊接参数,使良率从98%提升至99.5%,同时生成焊接质量报告,支持追溯与优化。
3. 多材料兼容:应对复合材质的CCS设计
为提升轻量化与散热性能,部分CCS开始采用“铜+铝+高分子材料”的复合结构。超声波焊接通过开发“多模式振动控制”技术(如垂直振动+水平振动组合),可同时处理金属与非金属材料的焊接,未来将成为复合CCS的标配工艺。
五、超声波焊接,为新能源电池“缝”出安全与效率
从“神经中枢”CCS的精密制造,到新能源电池的性能提升,超声波焊接正以其“冷、快、准”的特性,成为新能源产业链中不可替代的“隐形功臣”。随着技术的持续创新(如高频化、智能化)与行业需求的升级,超声波焊接不仅将推动CCS的性能突破,更将为“双碳”目标下的能源转型注入新的动能。
在这场新能源革命中,每一个精密的焊接点,都是通向更安全、更高效未来的“能量密码”。而超声波焊接,正用“无声的振动”,为新能源电池“缝”出更美好的明天。
六、超声波焊接机
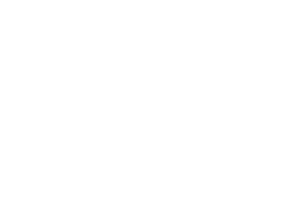
新能源汽车的快速发展带动了动力电池的高速增长。动力电池生产流程一般可以分为前段、中段和后段三个部分。其中,前段工序包括配料、搅拌、涂布、辊压、分切等,中段工序包括卷绕/叠片、封装、烘干、注液、封口、清洗等,后段主要为化成、分容、PACK等。材料方面主要有正负极材料,隔膜,电解液,集流体,电池包相关的结构胶,缓存,阻燃,隔热,外壳结构材料等材料。 为了更好促进行业人士交流,艾邦搭建有锂电池产业链上下游交流平台,覆盖全产业链,从主机厂,到电池包厂商,正负极材料,隔膜,铝塑膜等企业以及各个工艺过程中的设备厂商,欢迎申请加入。
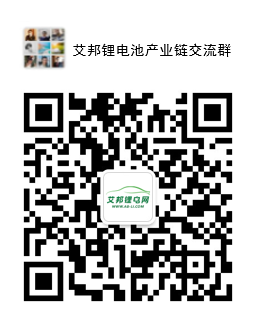
长按识别二维码关注公众号,点击下方菜单栏左侧“微信群”,申请加入群聊