随着新能源汽车及储能电池的发展,对铜箔及铝箔的需求日趋剧增,传统电解铜箔由于生产工艺复杂、成本高,难以满足新能源汽车对安全性的要求。由于工艺不成熟、设备投资成本高、制造成本高,制约了压延铜箔在国内市场的发展进程,产品基本被国外垄断。压延铝箔由于投资大、对生产环境要求高,难以大面积推广。
在此基础上,业内人士借鉴真空镀膜技术,吸收包装膜、电容膜的生产经验,结合磁控溅射国内关键技术和靶材的突破,在薄膜上蒸镀铝和铜技术在新能源汽车电池上的应用有了零的突破,并提出了复合集流体的概念。
表1 电池材料发展简表
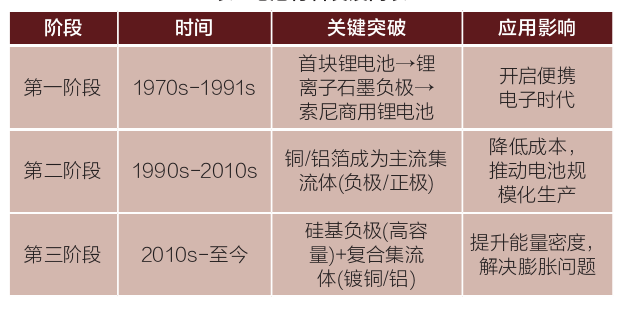
集流体是锂电池中铜箔和铝箔的总称,起承载活性物质和汇集电流的作用,我们可以理解为“面包”。而复合集流体,则是一个“三明治”,结构为“金属-PET/PP-金属”,即中间一层基膜,上下各镀一层1μm左右的铜,形成复合结构。
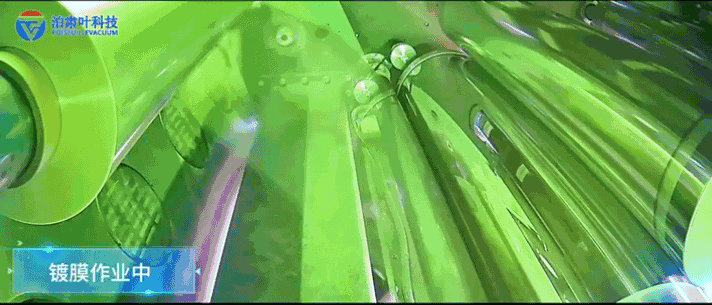
素材来源于泊肃叶
2、铜、铝复合材料常用的镀膜工艺
2.1 单炉(车)蒸镀工艺
此工艺主要用在玻璃等其他基体上镀铝或者难熔材料,如硅、铬、镉、石墨等。对于铝来说,采用卷绕式钨丝,将纯铝挂在钨丝上,通低电压大电流快速熔化。对于硅、铬、镉、石墨等难熔金属,采用真空下通惰性气体后用磁控电子枪对材料进行熔化,最终形成铝、硅、铬等原子蒸气,快速蒸镀到玻璃或者其他基体材料上。镀铝一般用在镜子或者车灯反光材料上,镀硅、铬、镉等材料主要用在镜片或者眼镜片上,典型应用为眼镜片、航空航天观察窗或者工业设备观察窗上。
镀石墨主要是在铜箔上,主要用于单层石墨的制作,最终用于石墨烯的研发。但此工艺生产效率低、成本高,不能连续生产、产量低,同时频繁地抽放真空,开关室门,容易造成设备故障及批件质量稳定性差。此种工艺主要用于小批量、非标化生产,在眼镜、车灯装饰等行业广泛应用。其主要优点是设备投资低,生产组织灵活,通过更换不同的挂具,或者采用AB车交替,即可实现多品种生产。
2.2 半连续蒸镀工艺
此工艺分为2种,一种为易熔金属,如锌、铝、锡等;一种是难熔金属,如铜、镍、金等。
(1)易熔金属镀膜
此工艺主要用于卷绕式薄膜镀铝或者镀锌等生产,采用连续送铝丝或者坩埚熔化锌锭的方式,将圆盘式铝丝装挂在专用挂具上,采用集中传动或者单独传动的方式,将铝丝送到蒸发舟上,蒸发舟一般情况下采用氮化硼和硼化钛高温压结而成。
在低电压大电流的情况下加热至可以将铝丝连续熔化,在高真空下,一般情况下真空度为4×10-4mbar(1mbar=100Pa),薄膜贴在-15~-10℃镀膜辊筒上或者前后2个冷却辊上,中间形成平板,在带张力的情况下高速运转,铝或者锌蒸汽在上下温差的情况下,以超音速的速度运动,快速打在薄膜上,形成致密的金属膜层,过程中可以通过方阻检测或者光学OD检测,来调整镀层厚度或者单通道的镀层厚度,以满足使用需要。
(2)难熔金属镀膜
此工艺主要用于卷绕式薄膜镀铜,采用磁控溅射靶材,在通惰性气体的情况下,将铜靶材电离成铜离子,在高真空下,一般情况下真空度为4×10-4mbar,薄膜贴在-15~-10℃镀膜辊筒上或者前后2个冷却辊上,中间形成平板,在带张力的情况下高速运转,铜离子快速运动附着在薄膜上,形成超薄的金属膜层,过程中可以通过方阻检测来调整镀层厚度以满足使用需要。由于磁控溅射需要电流大,效率较低,成膜速率慢,如果镀层较厚,需要多次往复镀膜来增加厚度。
2.3 几种镀膜形式的比较(表2)
表2 几种镀膜形式的比较
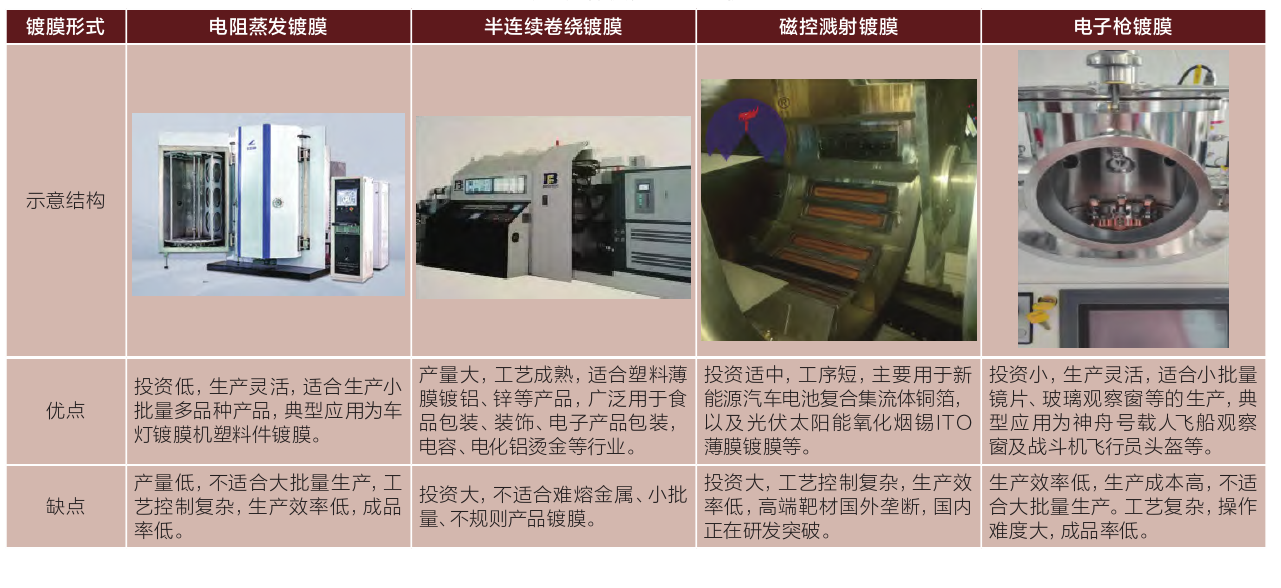
(1)电阻蒸发镀膜
-
优点:投资低,生产灵活,适合生产小批量多品种产品,典型应用为车灯镀膜机塑料件镀膜。
- 缺点:产量低,不适合大批量生产,工艺控制复杂,生产效率低,成品率低。
(2)半连续卷绕镀膜
-
优点:产量大,工艺成熟,适合塑料薄膜镀铝、锌等产品,广泛用于食品包装、装饰、电子产品包装,电容、电化铝烫金等行业。
- 缺点:投资大,不适合难熔金属、小批量、不规则产品镀膜。
(3)磁控溅射镀膜
-
优点:投资适中,工序短,主要用于新能源汽车电池复合集流体铜箔,以及光伏太阳能氧化烟锡ITO薄膜镀膜等。
- 缺点:投资大,工艺控制复杂,生产效率低,高端靶材国外垄断,国内正在研发突破。
(4)电子枪镀膜
-
优点:投资小,生产灵活,适合小批量镜片、玻璃观察窗等的生产,典型应用为神舟号载人飞船观察窗及战斗机飞行员头盔等。
- 缺点:生产效率低,生产成本高,不适合大批量生产。工艺复杂,操作难度大,成品率低。
3、新能源汽车电池用复合集流体优势
3.1 本质安全:高分子材料阻断热失控,杜绝电池起火风险
复合集流体的高分子层本质上是塑料材质,受到穿刺时产生的毛刺小,且高分子材料层会发生断路效应,可控制短路电流不增大,从而有效控制电池热失控乃至爆炸起火。这种结构形式能显著提高热稳定性,避免刺破电池隔膜,降低电池短路的风险,提升了电池安全性,做到了本质安全。
3.2 能量密度跃升:轻量化结构助力更长续航
通过优化集流体的结构和材料,复合集流体能够在保证电池性能的同时,提高电池的能量密度,提升电池的续航能力。此外,复合集流体的应用还预示着电池行业的技术进步和产业升级,为电动汽车等新能源设备的发展提供了更为有力的保障。
3.3 降本增效:减少金属用量,实现规模化成本优势
复合集流体采用高分子材料作为中间层,可以大幅度降低对于金属材料铜和铝的使用量,同时集流体整体重量相较金属铜铝也会大幅度降低,从而实现了降本增效。这种材料的使用不仅有助于降低生产成本,还有助于减轻电池重量,进而提升电池的能量密度。
复合集流体的发展为新能源汽车电池行业带来了革命性的变化,通过提高安全性、降低成本、提升能量密度等优势,推动了电池技术的进步和产业的发展。随着技术的不断成熟和市场需求的增加,复合集流体有望在未来扮演越来越重要的角色。
来源:胡亮,孙红刚,汪燕,孙长权,童裕文,.浅析新能源汽车电池复合集流体镀膜方式的选择【J】.汽车维修与保养,2025,(07):79-80.
新能源汽车的快速发展带动了动力电池的高速增长。动力电池生产流程一般可以分为前段、中段和后段三个部分。其中,前段工序包括配料、搅拌、涂布、辊压、分切等,中段工序包括卷绕/叠片、封装、烘干、注液、封口、清洗等,后段主要为化成、分容、PACK等。材料方面主要有正负极材料,隔膜,电解液,集流体,电池包相关的结构胶,缓存,阻燃,隔热,外壳结构材料等材料。 为了更好促进行业人士交流,艾邦搭建有锂电池产业链上下游交流平台,覆盖全产业链,从主机厂,到电池包厂商,正负极材料,隔膜,铝塑膜等企业以及各个工艺过程中的设备厂商,欢迎申请加入。
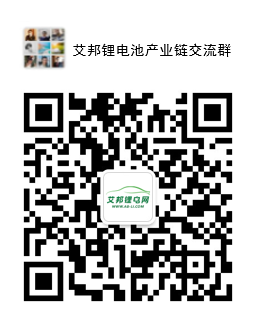
长按识别二维码关注公众号,点击下方菜单栏左侧“微信群”,申请加入群聊